Kevin J.
Brault
President
Sharp Technologies and Design Group
kbrault@sharptechdesign.com
http://www.sharptechdesign.com
480-899-5565
|
|
2011 to Present:
Sr Adv Mechanical Engineer 3 and ME Tools Administrator, General
Dynamics Mission Systems, Scottsdale, Arizona
Secret Clearance
Mechanical Engineering, CAD/CAS
Administration and
user support services.
|
|
|
- Support and lead engineer
on several programs for the deployment of satellite communication space
hardware while maintaining schedule and budget.
- Worked with Environmental
Test Group on Vibe, TVAC and Shock testing of development and fight units.
- Used ANSYS, CSL, CAS
and CS to refine designs, meet predicted minimum margins of safety on thermal,
modal, structural and fatigue requirements.
- Created and presented
documentation for PDRs and CDRs.
- Worked with IT, Manufacturing
and Supply Chain on automation and processes to reduce the cost and errors
in fabricating and inspecting components designed and procured. Process
creates a PDF file of the drawing and automatically embeds the required
2D and 3D data files (DXF, STEP).
- Worked with IT on
splitting the CAD PDM system into GD-C4S and GD-AIS companies.
- Assumed the role of ME
Tools Administrator (Creo, ANSYS, Pro/Intralink and Windchill) for ~30
users.
- Migrated from PTC
Pro/Intralink to Windchill.
- Merged six sites PLM CAD
data into Windchill.
- Number of supported
users now over 500.
- Deployed two
Simulation clusters and multiple high performance “shared” computers for
large and multiple simulations. Reducing the time to solution and design
margins for MEs.
- Developed and deployed
MCAD library process.
- Developed and deployed
the embedded PDF process on the server triggered by drawing state
changes.
- Developed and deployed
an automated process that drives the Parts List in windchill from the CAD
model structure. Reducing ME time and errors.
- Developed the processes
to make GD Model Based Definition (MDB, ASME Y14.41 and 14.47)
compliant.
- Currently working on a
multi-million dollar program to begin building “Digital Threads” and “Digital
Twins” for GD products.
|
|
2000 to Present:
President, Sharp Technologies and Design Group, Chandler
Arizona
Mechanical Engineering, CAD Administration and Network
Administration Services
|
|
|
- Successfully managed
seven independent, parallel projects and directed the efforts of six
engineers and designers to design and develop engineering solutions on
accelerated schedules for a variety of customers in the industrial,
commercial and aerospace industries.
- Created detailed
models and drawings in Pro/Engineer and SolidWorks.
- Provided Finite
Element Analysis using CosmosWorks and Pro/Mechanica.
- Manage CAD and other
data in Pro/Intralink, Windchill, Teamcenter and Subversion.
- Prepared proposals
including costing and scheduling estimates for various industries.
- Tray and pallet
handling and conveying equipment for the biochip industry.
- Tray, boat and pallet
handling, conveying and high speed pick and
place for the semiconductor industry.
- Silicon wafer
polishing (CMP), cleaning and handling equipment.
- Fixturing and
automated assembly equipment for the aerospace and consumer products
industries.
- Developed systems
software practices and policies to increase engineering department
efficiencies.
- Developed procedures
and software systems to organize concurrent engineering data among
engineers all over the world.
- Developed automated
document release systems that reduce cost, error and are ISO standards
compliant.
- Setup and maintain network
systems (Microsoft Small Business Server and Linux) that are cost
efficient for small and medium enterprises.
The following are a few of the projects I successfully completed:
|
|
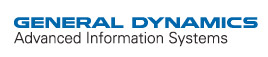
|
MCAD
Administrator, General Dynamics Advanced Information Systems
Automated steps in the design activity and developed new release and data control
mechanisms to enhance data integrity and reduce cycle and work time. Improved
modeling techniques to create more "intelligent" models, reducing
design and checking effort and errors and preparing the company for
"drawing-less" documentation. Performed Pro/Intralink 3.0 to 3.4
data migrations for two sites. Performed data separation for one site
(department split). Performed Pro/Intralink 3.4 to Windchill 9.1 migration
for two sites (Over one million objects, 510 GB of data).
|
|

|
Mechanical
Engineer, Honeywell Engines, Systems and Services
Brought “Out of the Box” ideas to solve new challenges. Utilized
Pro/Engineer and Pro/Mechanica to expedite the
design, reduce cost and minimize the mass of new control valves for the
Airbus A380 aircraft.
|
|
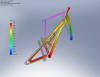
|
Senior
Analysis Engineer, Titus Cycles
Analysis Engineer Utilized FEA to validate and optimize bicycle frame
designs.
|
|
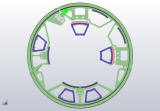
|
Senior
Mechanical/Analysis Engineer, Raytheon Missile Systems
Optimized Missile Fixturing/Lifting Ring for weight and strength using
Pro/Engineer and Pro/Mechanica. Fixture designed to
be configurable with adjustment components uniquely stored on the ring itself..
|
|
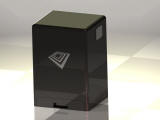
|
Senior
Mechanical Engineer, Akrometrix
Portable Moiré Flatness Measurement Machine: Unique sheet metal enclosure is
designed to maximize rigidity and minimize mass. The designed required a
stiff structure which was achieved without heavy frame members.
|
|
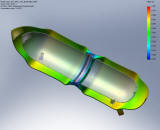
|
Senior
Mechanical/Analysis Engineer, Watts Premier
Potable Liquid Pressure Vessel: Utilized new materials and devised new
manufacturing techniques along with FEA to increase cost advantages over
current product.
|
|
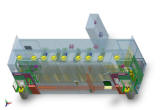
|
Senior
Mechanical/Analysis Engineer, MEMC
Wafer Handler in Wafer Cleaning System: Replaced complicated and troublesome
bulk wafer transfer system with six axis robot and load port. Analyzed motion
with Pro/Mechanism.
|
|
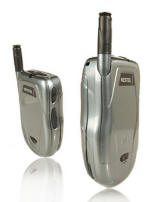
|
Senior Mechanical Engineer, Motorola
Cell Phone Product Releases:
- Produced solid
production models and drawings from Industrial Engineering surface
models.
- Worked with electrical
engineers to mechanically package electronic components.
- Evaluated other
designs for technology reuse and improvement.
- Evaluated first article
QC reports, performed accelerated life tests and provided corrective
action recommendations. Worked with Engineers in Florida and China on
issue resolution.
- Reduced Accelerated
Life Test cycle time and variability by improving the test process.
- Optimized rigidity by
utilizing Pro/Mechanica.
|
|
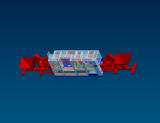
|
Lead
Project Engineer, Rainbird
Automated Sprinkler Head Assembly Machine: Machine assembled and inspected
six components to produce a finished product every two seconds. Managed six
engineers and designers to meet schedule and performance requirements for the
$730,000 project.
|
|
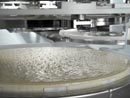
|
Senior Mechanical Engineer/CAD Administrator, Novellus
CMP equipment for the Semiconductor industry:
- Provided Pro/Engineer
and Pro/Intralink support and training to 28 member staff. Developed
automated document and CAD data release procedure. Simultaneously
supported design efforts on new CPM products.
- Wrote software to
analyze license logs and negotiated a 34% reduction in software product
maintenance costs to save the customer $230,000 annually.
- Provided cost return
analysis for hardware upgrades increasing engineering efficiency.
- Developed Pro/Engineer
scripts to automate repetitious operations reducing modeling time and
design errors while standardizing design and drawing methods.
- Implemented an
automated “PDF” process where drawings are automatically printed to a
“PDF” file, watermarked with a “Released” stamp and pulled into a data
access system. Reducing Engineering work load and providing “Released”
documents to the whole organization within 20 minutes of approval.
- Developed automated
process and software to “push” Bill of Material data from the
Pro/Engineer to an MRP system. Eliminated the need to “Release” a BOM
under an ECO. Reducing engineering work load and updating MRP
information in less than 20 minutes. Automated rollout of new software
releases. Reducing Engineering interruptions.
|
|
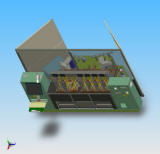
|
Lead
Mechanical Engineer, Unaxis
High Speed JEDEC Tray Substrate Pick and Place: The challenge met was to
rapidly load and unload JEDEC trays with new, good and failed devices with
two, four axis SCARA robots while simultaneously staging and re-ordering non-WIP
trays.
|
|
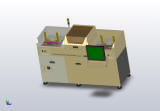
|
Lead
Mechanical Engineer, Sonix
Automatic Ultra-sonic substrate Inspection Machine
|
|
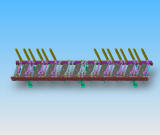
|
Lead
Mechanical Engineer, Unaxis
Sideways JEDEC Tray Handler
|
|
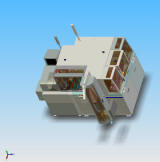
|
Lead
Mechanical Engineer, Motorola
Substrate Singulation machine: Successfully merged two separate technologies
(wafer dicing and JEDEC tray loading) to produce a machine that replaced two
pieces of equipment and reduced cycle time and floor space.
|
|
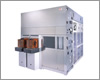
|
Mechanical
Engineer, Speedfam
CMP equipment for the Semiconductor industry: worked with supplier in Israel
and customers in Europe to retrofit the CMP tool with inline inspection
systems.
|
|
1997 to 2000
Staff Engineer, Motorola Manufacturing Systems - Phoenix, Arizona
Division of Motorola producing automated manufacturing equipment for the
semi-conductor industry.
|
|
|
|
Reported
to the Engineering Manager for the design, development and project management
of automation and BGA manufacturing equipment projects. Responsible for
Pro/ENGINEER (Rev 17 – 2000I) and Pro/PDM (Rev 3.5) software and hardware
administration (UNIX and NT).
|
|
|
- Generated engineering
concepts through final designs, work with vendors and customers to bring
innovative automated equipment solutions to semi-conductor manufacturers
worldwide.
- Worked with
engineering team to bring to market a new substrate singulation machine
generating ~$700,000 per month in sales.
- Developed automatic
tool alignment system that reduced machine setup time by more than 70%.
- Led team to design and
develop a manual solder sphere attachment machine for CBGA scale
wafers/substrates that can place 200,000, 0.3 mm diameter spheres in 3
minutes on a 300 mm wafer.
- Orchestrated project
team with engineering, customers and manufacturing to reduce the cost of
second generation wafer BGA machine by 40% and
make a mass-marketable product.
- Worked with engineers
in other countries to develop advanced BGA sphere attachment process for
$1.2 million order.
- Developed new
technologies to reduce production lead time (50%) and cost (30%-70%) of
sphere attach tooling.
- Reduced number of
unique parts while increasing performance.
- Redesigned conveyor
system and reduced cost by 60% and lead time by 67%.
- Specified and
implemented computer hardware upgrades to reduce engineering time and
administration costs.
- Converted computer
platforms from UNIX to NT.
- Worked with four other
sites to develop common engineering practices and software/model
libraries.
- Provided Finite
Element Analysis (FEA) of critical components Using Pro/Mechanica.
|
|
1995 to 1996
Project Engineer, Ryobi Outdoor Products - Chandler, Arizona
Lawn and Garden and Power Tool Manufacturer with locations in the United
States, Mexico and Japan.
|
|
|
|
Reported
to the Director of Engineering for the design, development and evaluation of
hand-held lawn and garden products. Utilized Pro/ENGINEER CAD-CAM software
(UNIX and NT Operating Systems) to design new products with common features
and parts, resulting in fewer manufacturing and production changes.
|
|
|
- Generated Pro/ENGINEER
part models that were "Family Driven", simplifying and
reducing engineering design time on new, similar components (primarily
die-cast and injection molded), and thus, bringing new products to
market faster.
- Evaluated, upgraded
and automated data acquisition hardware and software for emissions
equipment resulting in increased accuracy of data and rapid production
test evaluations.
- Performed extensive
tolerance studies of several similar assemblies resulting in design
changes that reduced the number of new components and assemblies and
thus reduced inventory and tooling cost.
|
|
1990 to 1995
Application Engineer - Small Engines, INA Bearing Company, Inc. - Fort
Mill, South Carolina
The world's largest producer of needle roller bearings.
|
|
|
|
Reported
to the Application Engineering Manager for the calculation, design and
proposal of roller bearing arrangements, through development of samples,
production start-up, and customer support including bearing failure analysis
and corrective action proposals.
|
|
|
- Worked with Field
Sales and Product Engineering on customer accounts totaling over $15
million, increasing sales by 78% in four (4) years, and increasing 1994
sales by over $3 million (31%), exceeding the 25% forecast.
- Generated bearing
proposals and Structural FEA's and provided engineering support to a
customer, resulting in acquiring a three million
dollar account from a competitor.
- Developed computer
engine simulation software to increase the accuracy of bearing life
calculations in conjunction with developing statistical tolerance
standards for connecting rod assemblies.
|
|
1987 to 1990
Project Engineer, Force Outboards (Mercury Marine) - Division of Brunswick
Corp. - Hartford, Wisconsin
A $150 million division producing marine outboard propulsion drives.
|
|
|
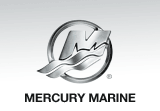
|
Reported
to the Director of Engineering for the design, development and introduction
of new products and product improvements on the 5, 9.9, 15 and 25 horsepower
outboards.
|
|
|
- Designed and developed
new porting, piston (Thermal FEA), reed valve and starting system on 5
HP engine, increasing power output by 30%, reducing RFI emissions, reducing
cost by $7 per unit and increasing life by 200%.
- Developed a
Pro/ENGINEER CAD solid model of the 25 HP combustion chamber and
crankshaft, eliminating experimental prototypes and reducing product
development costs and lead times.
- Developed new reed valve
assembly on 90 through 150 horsepower models reducing the number of
components by 10%, cost by 17% and increasing performance by 5% to 8%.
- Implemented Concurrent
Engineering with manufacturing engineers and vendors on the 25 HP
project, reducing production costs, capital costs, tooling lead times
and engineering changes.
- Utilized common vendor
products and existing in-house fixturing and assembly stations common
with other product lines.
- Generated and
maintained Bills of Materials for the 5, 9.9, 15 and new 25 HP model
lines and supervised the efforts of up to three (3) designers and three
(3) technicians.
|
|
Education:
|
|
|
Bachelor
of Science Degree - Mechanical Engineering - 1987 University of Wisconsin -
Madison
|
|
PTC
|
Pro/Engineer
Basic and Advanced
|
|
Professional Affiliations:
|
|
|
Phoenix
Pro/Users Group - Chairman
|